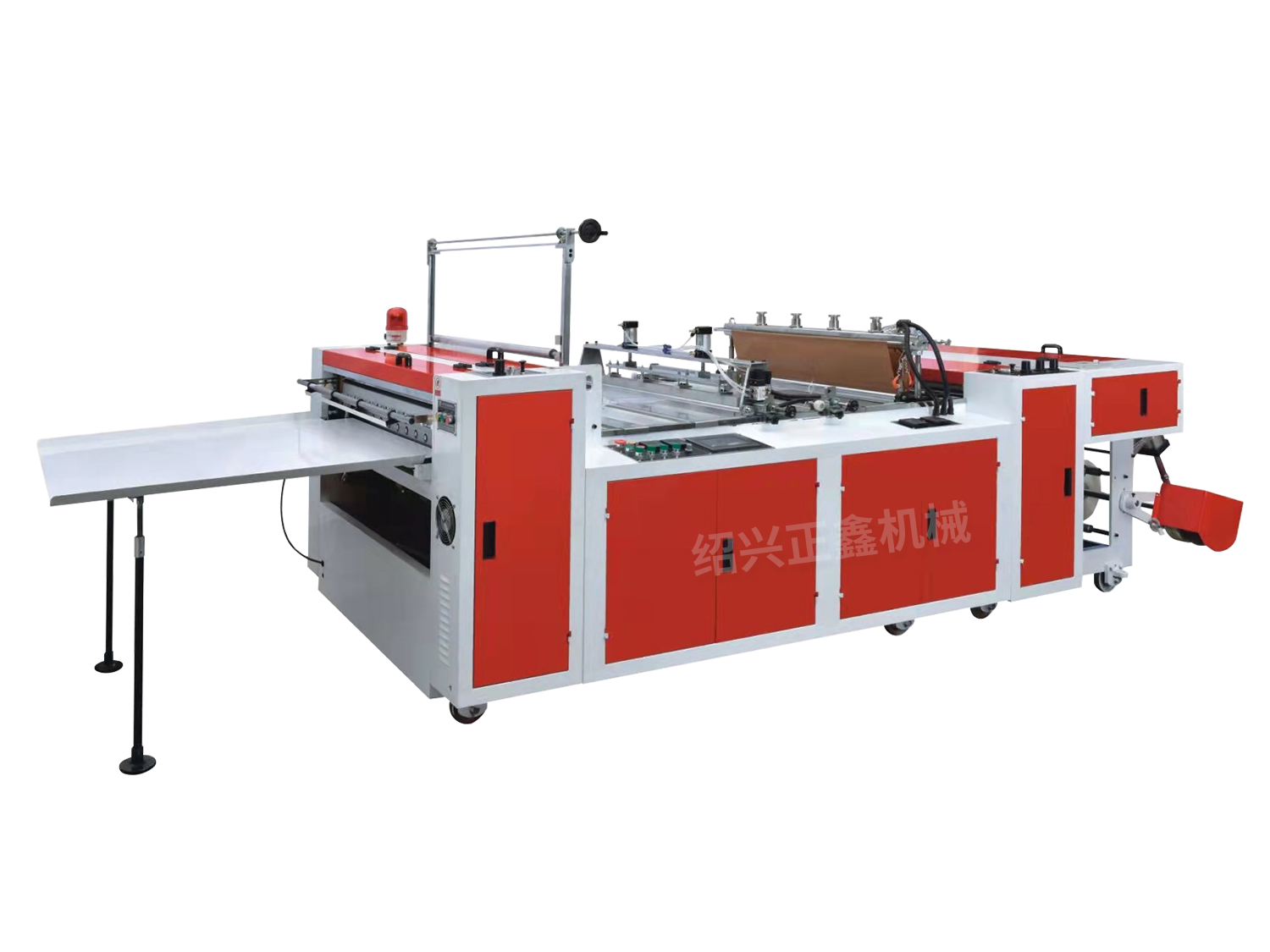
Understanding Cold-Cutting No-Tension Bag Making Machines
Cold-cutting no-tension bag making machines are a significant departure from their predecessors. They utilize innovative technology that eliminates the need for heated cutting blades and the tensioning of materials during the bag-making process. Instead, these machines use ultrasonic or mechanical methods to cut materials cleanly and precisely, without generating heat.
Key Features and Advantages
Precision Cutting: Cold-cutting no-tension bag making machines employ ultrasonic or mechanical blades that produce clean and precise cuts. This eliminates jagged edges and irregular shapes, resulting in higher-quality bags.
Reduced Material Waste: Traditional tension-based bag making machines often generate considerable waste due to uneven cutting and trimming. In contrast, cold-cutting machines produce bags with minimal trim, significantly reducing material waste.
Enhanced Durability: The absence of heat during the cutting process means that the bags produced are less likely to have weakened or melted edges, making them more durable and reliable for packaging a wide range of products.
Increased Productivity: Cold-cutting machines can operate at faster speeds compared to their traditional counterparts, leading to increased productivity and reduced production time.
Versatility: These machines can work with a variety of materials, including plastics, paper, non-woven fabrics, and more, making them versatile and adaptable to various bag manufacturing needs.
Energy Efficiency: Since cold-cutting machines do not require heated blades, they consume less energy, contributing to sustainability efforts and reducing operating costs.
Applications
Cold-cutting no-tension bag making machines are finding applications across a range of industries:
Retail Packaging: These machines are ideal for producing high-quality shopping bags, reducing the need for rework or wastage.
Food Packaging: The precision and cleanliness of cold-cutting make it suitable for producing food-grade bags, ensuring the safety and freshness of products.
Medical and Pharmaceutical Packaging: The precise cutting and reduced material waste are essential in these industries where precision and sterility are critical.
Agriculture: Cold-cutting machines are used to produce seed bags, fertilizer bags, and other agricultural packaging, ensuring durability and reliability.
Environmental Sustainability: The reduction in material waste and energy consumption aligns with environmental sustainability goals, making these machines an eco-friendly choice.