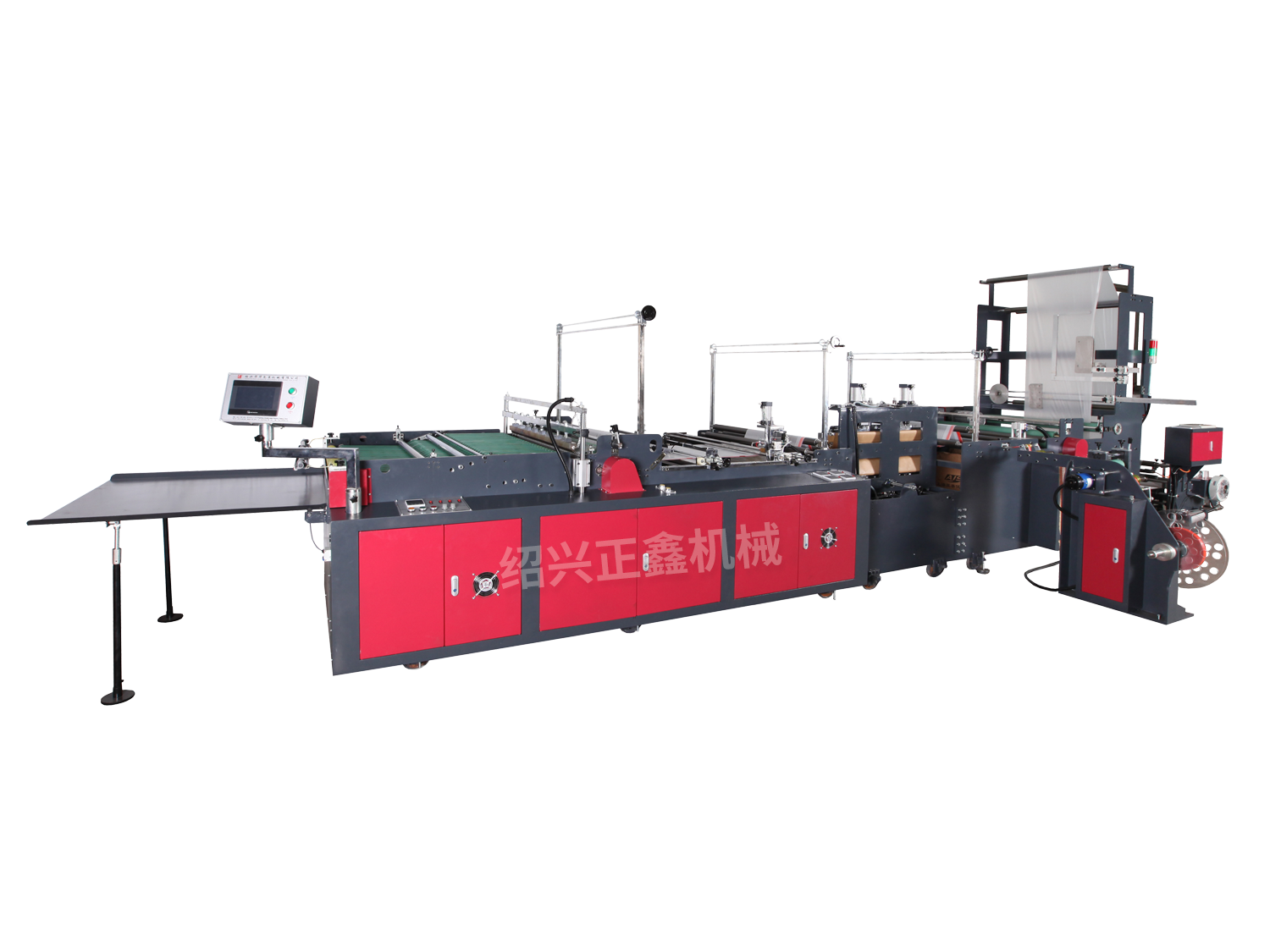
The operating procedures of the bag making machine
Operating procedures of the bag making machine:
1. Preparations before starting
1. Check whether there is dust and debris around the equipment and remove them.
2. Install the film roll according to the requirements of the production notice.
3. Adjust the size of the bag according to the production notice and process documents, install the heat sealing knife, and preliminarily adjust the position of the slitting knife and the heat sealing knife.
4. Turn on the power and set the temperature of the heat sealing knife according to the requirements of the process document.
5. Input the relevant data of bag making and the required number of each bundle.
6. Select the edge of the pattern with large color difference and adjust the sensitivity of the light eye to make it meet the requirements.
2. Start
1. Start the main motor, run at low speed, and then adjust the edge position control to divide the film in the middle position.
2. Adjust the left and right pinch rollers to align the left and right films, and adjust the front and rear pinch rollers to align the pattern.
3. Adjust the heat-sealing knife to make it heat-sealed within the required range of the bag.
4. Adjust the slitting blade to the desired position, and adjust the punching position to the scissors mouth.
5. Preliminarily adjust the speed of the machine, take a flat-out sample bag for initial inspection, and if it does not meet the specified requirements, take another flat-out sample bag for heat sealing value test.
6. Arrange the produced bags, and select the bags with quality defects (such as folding, tunnel, flower width, knife line, poor heat sealing, four seals, etc.) and bundle them according to regulations.
7. The machine quality inspector will carry out the inspection. After the inspection is qualified, the certificate will be pasted and sent to the quality inspection room for random inspection.
8. During the production process, observe the bag making situation at any time and find any abnormality and adjust it immediately.
3. Stop
1. Disconnect the main power switch, and then disconnect the power switch of each part.
2. Clean the machine hygiene and site hygiene, and send the products to the general inspection room.
3. Make a record of the shift, which is required to be accurate and clean.
4. Packing
1. Packing: The machine personnel will sort out the products in this process, select the unqualified products with quality defects (such as folding, tunnel, flower width, cutting line, poor heat sealing, four seals, incomplete patterns, etc.) The product is bundled and handed over to the machine quality inspector for inspection.
2. Inspection: The quality inspector of the machine will inspect the quantity and quality one by one. After the quantity and quality are all qualified, they will be put into the box according to the requirements and put into the packing list; Qualified" marked in the carton.
3. The machine personnel will send the products on duty to the appearance quality inspection room.
4. The general quality inspector will sample and inspect the products submitted for inspection according to the specified proportion, and pack them into storage after passing the inspection.